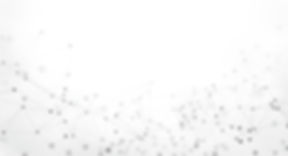

OEM Service
Manufacturing Service


PCBA Assembly- Quick Turn and Mass Production
Our manufacturing experiences and capabilities include:
-
Surface-mount technology (SMT)
-
Wave Soldering and Selective
Wave Soldering -
Passive component:
size down to 01005 -
BGA and µBGA: more than 4300 IO
-
IC: pitch down to 0.24mm
-
Chip-on-board (COB) and
System-in-Package (SIP) -
PCB, FPC, Rigid-flex
-
Press-fit
-
Static and Dynamic Burn-in test
-
Aqueous cleaning and Non-clean
processes -
Lead and lead-free production

Box-Build, System Integration, and Packing
-
Customized fixtures and jigs
-
Mechanical parts design recommendation and manufacturing
-
Packing design
-
Hardware and Software testing solutions

Inspection and Testing devices include:
-
Solder Paste Inspection (SPI)
-
Automated Optical Inspection (AOI)
-
Automatic Test Equipment (ATE) and In-circuit Test (ICT)
-
Flying Probe
-
X-ray Inspection
-
ERSA Scope
-
Function Test
-
Burn-in Test
Engineering Service
New Product Introduction (NPI)
-
LCE’s NPI center consists of engineering, quality assurance, material, and production management departments to keep every step of production on the right track.
-
Provide customers with DFM and DFT reports.
-
Product engineer acts as a coordinator to communicate issues with internal teams and customers, and to integrate internal information for solving problems timely.
-
Based on the NPI result, LCE’s NPI team then will provide improvement suggestions in pilot run report to expedite entering the mass production stage and launching products in the market.
Design for Manufacturability (DFM) and Design for Testability (DFT)
-
DFM (Design for Manufacturability)
Before taking your product to the mass production stage, our engineering team will inspect and evaluate your product for manufacturability. Via DFM report, we can assist customers identify design problem, reduce repetitive verification, save material and labor costs, expedite production and optimize product quality. -
DFT (Design for Testability)
Based on Gerber file analysis and past experiences, LEC’s engineering team can learn the PCB test coverage rate and verification failure risk during PCB layout stage. We then will work with your design engineers to modify circuit diagram for reducing possible issues caused by engineering changes.
ECO/ECR/ECN
-
ECO (Engineering Change Order) — initiated by RDs from customer side to modify design issues.
-
ECR (Engineering Change Request) — initiated by EMS, such as requiring customers to change components for improving SMT/DIP/assembly yield rate.
-
EECN (Engineering Change Notice) — issued by DCC (Document Control Center) to notify relevant departments of BOM been changed.

IPC-A-610 Class 3 Technology(1)
Class 3 Technology, established by IPC, is a standard of PCBA assembly and acceptance for special electronic products. This technology is applied in special fields such as Military, Medicine and Aerospace. For using these reliable instruments and devices under any conditions, they need to conform to more strict production standard as they are usually applied in extreme environment or concerning of human life.
Compared to IPC-A-Class 3 standard, LEC possesses more advanced electronic product manufacturing standard with High Reliability, High Temperature, and Extreme Environment. Nowadays our product applications provided by manufacturing service are Drilling Tool and Drilling Rig used in Drilling Platform, Satellite and satellite verification devices, etc. We also can offer customized manufacturing service based on customers’ requests.
PC-A-610 Class 3 Technology(2)
LEC’s IPC-A-Class 3 manufacturing abilities include:
-
Forming, Stripping and Tinning, Clinch
-
Soldering process: High Pb, High Au, Lead and Lead free processes
-
Clean process: Aqueous Cleaning and Solvent Cleaning
-
Staking
-
Conformal Coating, Encapsulation and Underfill
-
Swage terminal and standoff
-
Production fixtures/jigs research and development
-
Class 3 inspection

Materials Management
Material Planning
-
Adjust customers’ demand and provide planning strategy through SAP.
-
Consigned and Turnkey components management.
-
Manage materials supply via custom inventory simulation reports.
-
Provide regular material reports to keep customers informed of material status such as inactive ,obsolete and EOL parts.
-
Maintain safety stock or recommend alternative suggestion for critical materials.
-
Schedule materials delivery flexibly based on market condition to ensure supply smoothly.
Supply Chain Management
-
Make strategic planning for materials quality and cost.
-
Keep good relationships with suppliers for stable supply status.
-
Understand suppliers’ quality systems and production process to ensure material quality.
-
Audit suppliers’ quality, price, and delivery schedule regularly.
-
Enhance communication efficiency between LEC, customers and suppliers through the delivery platforms.
-
Share experiences and marketing information with suppliers to build win-win partnerships.

Warehouse Management System
-
Integrate data management of both suppliers and actual materials receipt through System.
-
Ensure daily warehouse operation smoothly.
-
Maintain inventory storage, FIFO (First-in-first-out) management.
-
Re-tapping and materials date code control management.
-
Materials traceability and stocktaking management.
Commitment to Quality
LCE is committed to provide our customers with the best products and services through collaborative teamwork, technological innovation and continuous improvement.

Commitment to Quality (International Standards)
Our certifications attest our commitment to comply with international quality and environmental standards.
We work, however, to not only comply with these standards, but also continuously improve the effectiveness of our entire quality management system.Compliance with TAA (Trade Agreement Act).
Quality Control Process
LEC systematizes the quality control process. We uphold the spirit of TQM (Total Quality Management) to provide training for quality control personnel and online operators, so that employees can understand various operation standards and specifications, from IQC (Incoming Quality Control), IPQC (In-Process Quality Control) to OQA (Outgoing Quality Assurance).
LEC ensures quality control of each production process for our valuable customers.


Quality Control Process
We understand the importance of preventing defected products rather than removing them after production.
Our proactive mindset ensures that no time or resources is wasted on unnecessary problems.
-
Production Process Design and Audit
-
Operators regular on-site training and verification
-
Statistical Process Control (SPC)
-
Continuous Improvement Programs

Commitment to Quality (International Standards)
Our certifications attest our commitment to comply with international quality and environmental standards.
We work, however, to not only comply with these standards, but also continuously improve the effectiveness of our entire quality management system.Compliance with TAA (Trade Agreement Act).